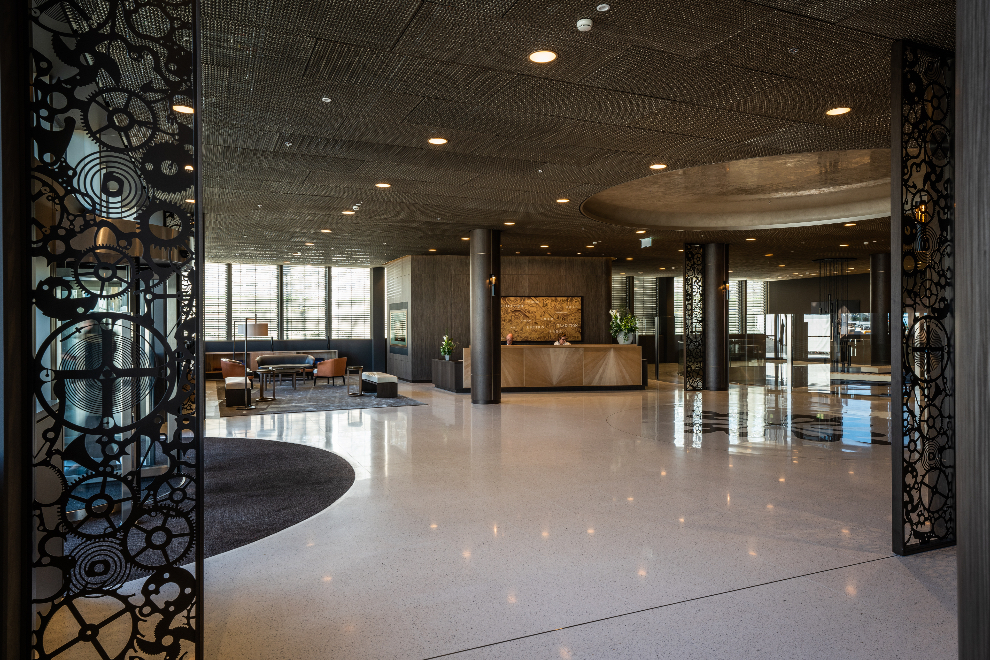
You know how sensitive the topic of production is, if you have any experience in the watchmaking industry. If you read about a new massive structure being built by watchmaker A, it is natural to wonder how many watches will be produced under this roof. Now, if you know a little more about watchmaking, it will not surprise you to learn that more watches are not on the cards – at least not right away, but certainly never to the extent that production will suddenly double.
While visiting the new Patek Philippe facility in Geneva’s Plan-les-Ouates neighbourhood (affectionately known as Plan-les-Watches or Plan-les-Watch), we are shown a staggering number of CNC (computer numerical control) machines. The press tour was organised for Southeast Asia journalists, and it was a real show-stopper for all of us, who knew that CNC machines could run 24 hours a day. This writer briefly considered how many brass movements blanks the new PP6 facility could produce with its multi-axis machines. This moment of foolishness passed quickly, however, as Patek Phlippe informed us that the finishing on gears, arbours, and pinions (also produced at the PP6 facility, using different CNC machines, in a bar-turning process where raw material bars are turned but the tools remain fixed) must be done by hand. Anything with teeth. It means, to put it bluntly, that every spoke on every wheel receives individual attention.
Pulling back a little from this specific close-up, the reality of watch manufactures is often surprising because these sites are often huge – the new facility we visited stands 34m high, with 10 storeys (four are underground, which Patek Philippe literally describes as subterranean, in good old secret lair style) for a total of 133,650sqm. Obviously, the site is massive yet Patek Philippe’s production volume of 70,000 watches (that is the top-end estimate; Patek Philippe does not disclose specific production numbers). What is required here is an establishing scene, so let us take you back to 2019, in the Before-Times – let us go back even further than this, for a bit of context.
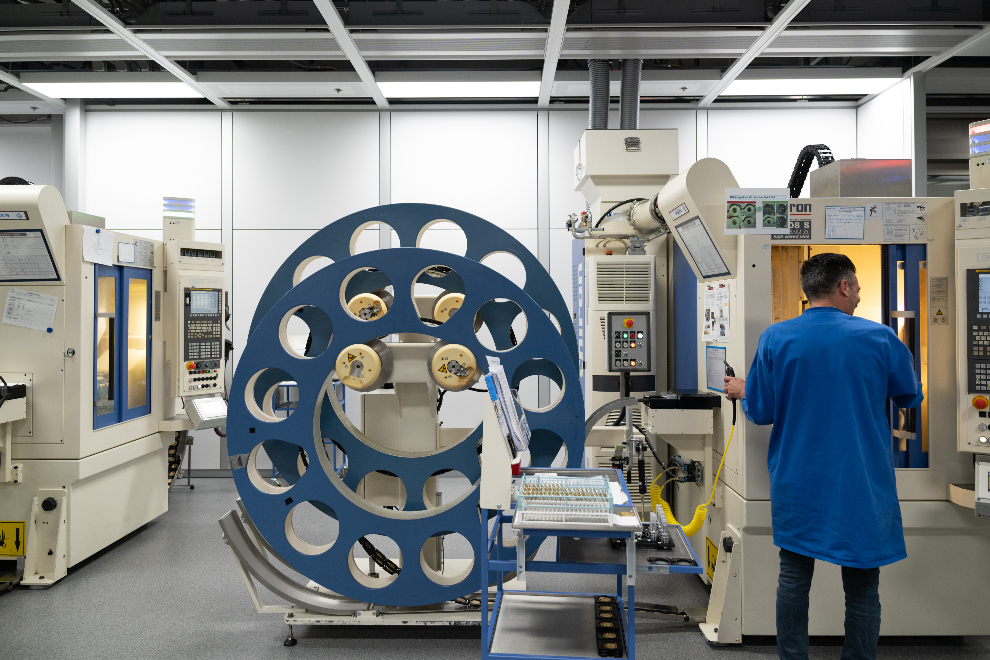
In The Beginning…
Since the founding of the company in 1839 and the Stern family’s takeover in the 1930s, Patek Philippe is on a mission to enhance and expand its capabilities. Over the years, wealth has become more accessible and more people are wearing timepieces. Bear this in mind when you visit the Patek Philippe Salons in Geneva – one of three owned and operated by the brand itself – because this space used to house the watchmakers. When the advent of quartz technology put paid to many a storied name, and even sent the watchmaking trade into decline, those firms that soldiered on – Patek Philippe amongst them – found that they had to take steps to protect the entire industry. As a matter of fact, the Patek Philippe Museum occupies a space formerly used by one of its suppliers, now turned in-house division – the famed bracelet-maker Ateliers Reunis. While both Salons and Museum are impressive, they cannot compare with the most recent addition to Patek Philippe’s manufacturing facilities.
Thierry Stern, the son of Philippe Stern, was already building on his father’s work when he became President of Patek Philippe. In 1996, the elder Stern announced that a new manufacturing facility would be built at Plan-les-Ouates. It was completed by 2009 when the younger Stern assumed the presidency. Patek Philippe needed to expand its facilities. They were modern but not up to date with the future. The solution came in several stages. Work on the building PP6 (the topic of this article) started in 2015. Clearly, Thierry wanted something grand, and PP6 is the perfect fit. We are not interested in this story as such, but rather what it might reveal to collectors and those who have yet to receive a Patek Philippe.
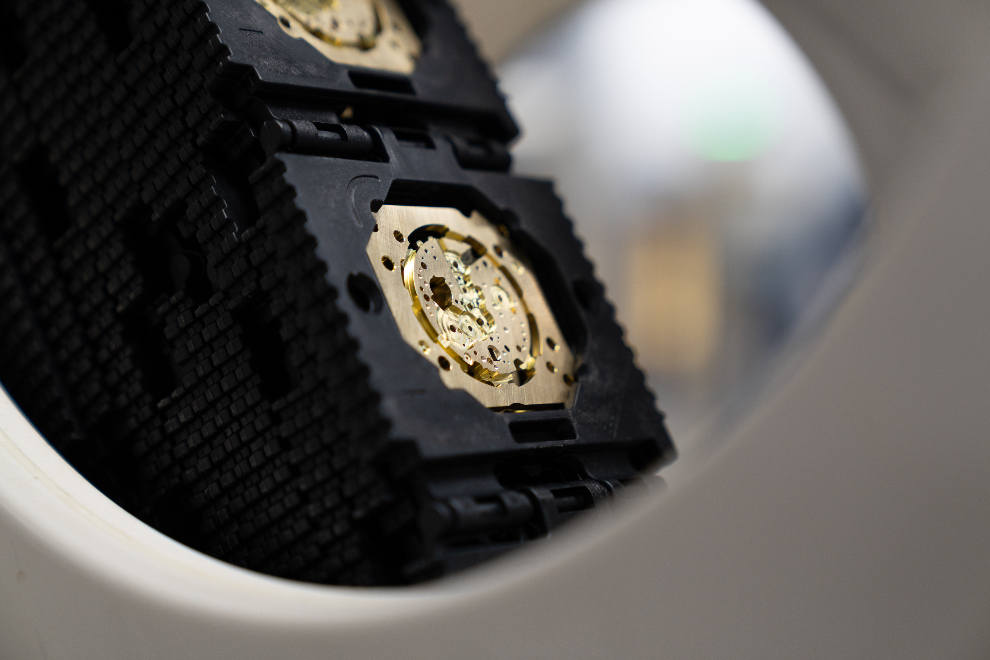
Patek Philippe has a unique way of working. It’s not that Patek Philippe has a unique manufacturing process or anything like that, but rather a method of work that is rational and logical. It is important to note that the plates are not made for complex movements. However, the teethed parts are used by all calibres. Plates and bridges are produced by different machines for complex watches. Why? We know and have been told that plates and bridges are thicker in complicated movements. They are then filed to the correct dimensions (still thicker) as skilled craftsmen can handle more complicated and delicate movements than CNC machines.
Worked by Hand
The tourbillon is an excellent and widely used example because the rough portion is very intensely worked by hand. The extra material helps to reduce minor mistakes, which are unavoidable. Gears and pinions, on the contrary, can be produced to a single standard specification. This writer has had to deal with errors in the past, as there are tolerances that are too tight for the naked eye. Suffice to say here that those who are looking for reasons why Patek Philippe might be production-limited – even with automated processes in the mix – can find one important point in the hobbing process, and what follows after. Hobbing is a technical term used to describe the production of teeth in parts.
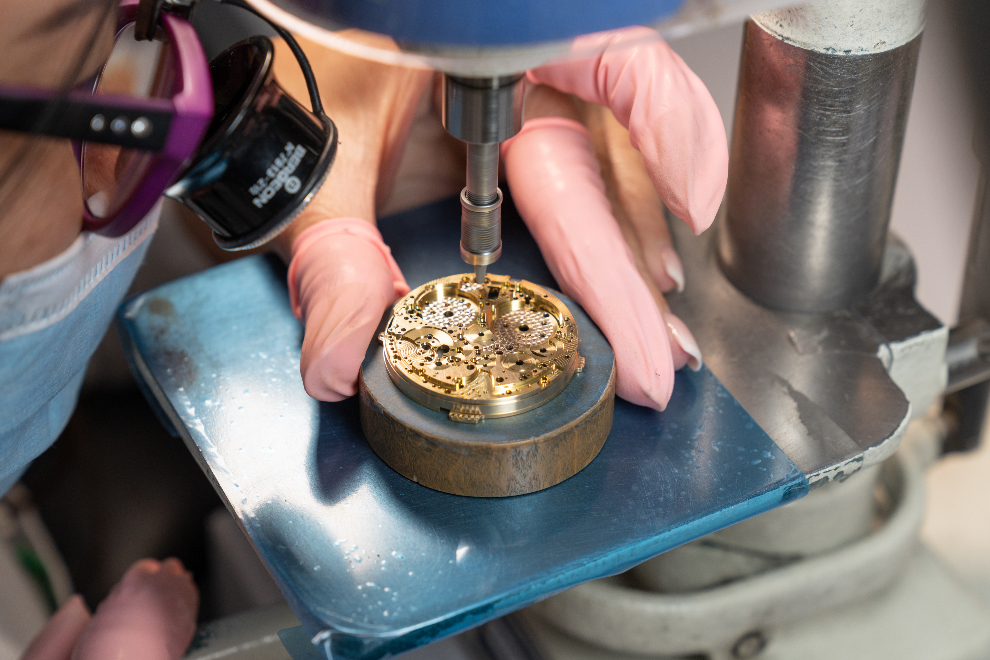
Unfortunately, space-constraints limit us as much as they do a watchmaker such as Patek Philippe, so we must move on for a little bit to bracelets and metiers d’art. This was not the time to talk about the movement assembly. It is actually done in another building at the Plan-les-Ouates manufacturing. We would also be remiss if we did not mention that the Advanced Research Department at Patek Philippe is located on the third-floor of PP6. Unfortunately, it was not part the tour. We hope, however, that in the future, it will. No reason should be given to complain about having a good reason to visit the Patek Philippe manufacturing.
We now move onto bracelets, which will be popular in the world of watch enthusiasts. All the bracelets in production we saw were for. Nautilus, which might be tied for most exclusive and most famous watch bracelet in the world – the GOATs of bracelets, one might say. The bracelets are always fascinating to watch, as they take shape link by link. Although, it is important to note that the raw materials arrive in the form a bar with the rough dimensions needed (with a groove on the middle). Patek Philippe took a lot of time in order to learn all 55 steps that go into making the Nautilus bracelet. You might be wondering why there is so much fuss about bracelets, but Patek Philippe was the only manufacturer we visited that showed us how they make their bracelets. Patek Philippe, unlike most other watch brands, has been producing bracelets in-house for many years.
Case Study
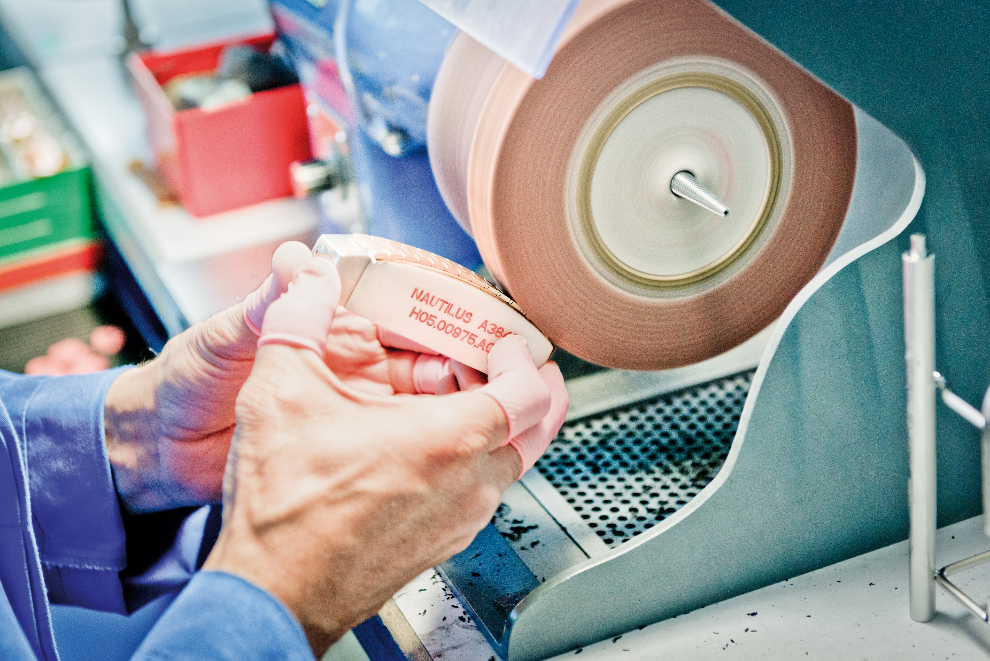
For the next step in the bracelet-making process, the shaped bar is sent to a bar-fed machining center. This will form the individual links. To keep it simple, this is a milling procedure that involves many quality control steps and hand-corrections, but they are not included in the 55 steps. As you know, there are two main parts to the bracelet links – the H-shaped bit and the centre link – and these are individually worked before being assembled (with pins). Even after the links have been assembled, buffing, chamfering, and polishing the centre links to the signature finish is required. The H-links are protected with perforated tape, and the entire length of the bracelet is polished.
We have enough room to discuss another Patek Philippe signature: the hobnail middle case decoration. (This can also be seen on bezels at times). Clous de Paris is achieved with a plane and comb lathe. It is up to you to visualize the correct technique to maintain pressure (the lathe stays still while the part moves). The process of making the case itself is fairly straightforward, with milling, polishing, and bar-turning. Patek Philippe has invested heavily to develop their own case-making capabilities.
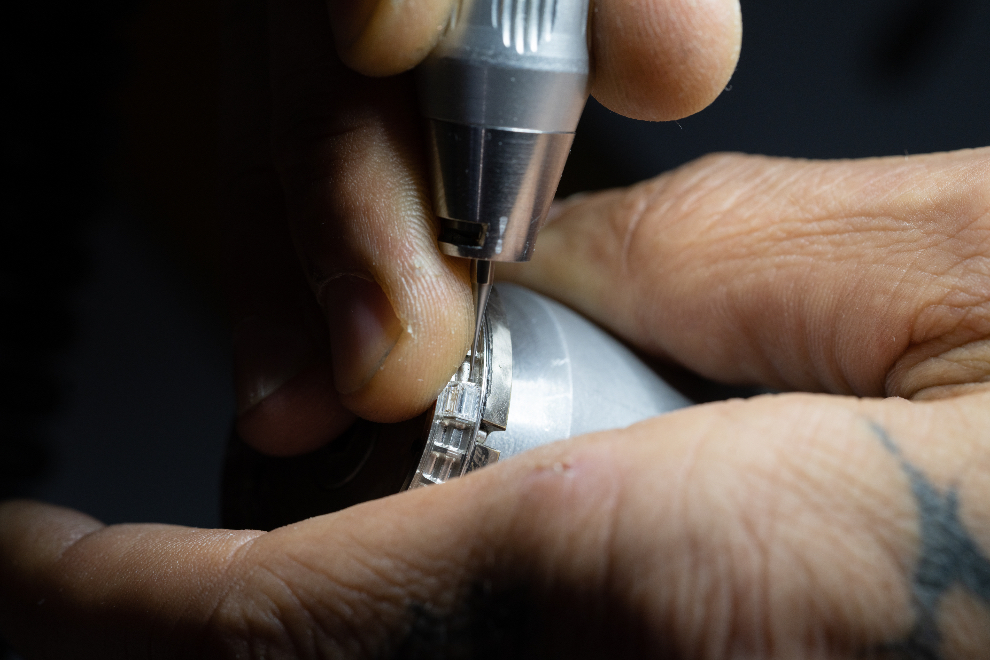
We will leave the final word to Rare Handcrafts even though this means that we have to leave the complications early and only have a few words left in captions for gem-setting. The tour included a demo of champleve, one of the 12 enamelling techniques that are used by all enamellers in Patek Philippe. As you can see, the champleve technique involves using paint to fill in the lines of a dial.
If you were to visit the Grand Exhibition, a demonstration of every technique would take either a few minutes or days. [in Tokyo or in Singapore in 2019]This part of the tour resembles that segment) and it is important to remember that Patek Philippe has also other artisans who work on dials in St. Imier at dialmaker Cadrans Fluckiger. Some of you have probably seen Anita Porchet in Singapore or heard her speak. It also employs external specialists like Anita Porchet.
In that sense, Patek Philippe is like a home for watches. They are prepared with love and care to be sent into the world. The next time you see your Patek Philippe watch, spare a thought. Someone at home in Geneva may be trying to imagine the joy you will find in it. This story may convince you that it’s worth a Patek to get closer.
This article first appeared on WOW’s Legacy 2024 issue
Click here to learn more about the latest watch readings.