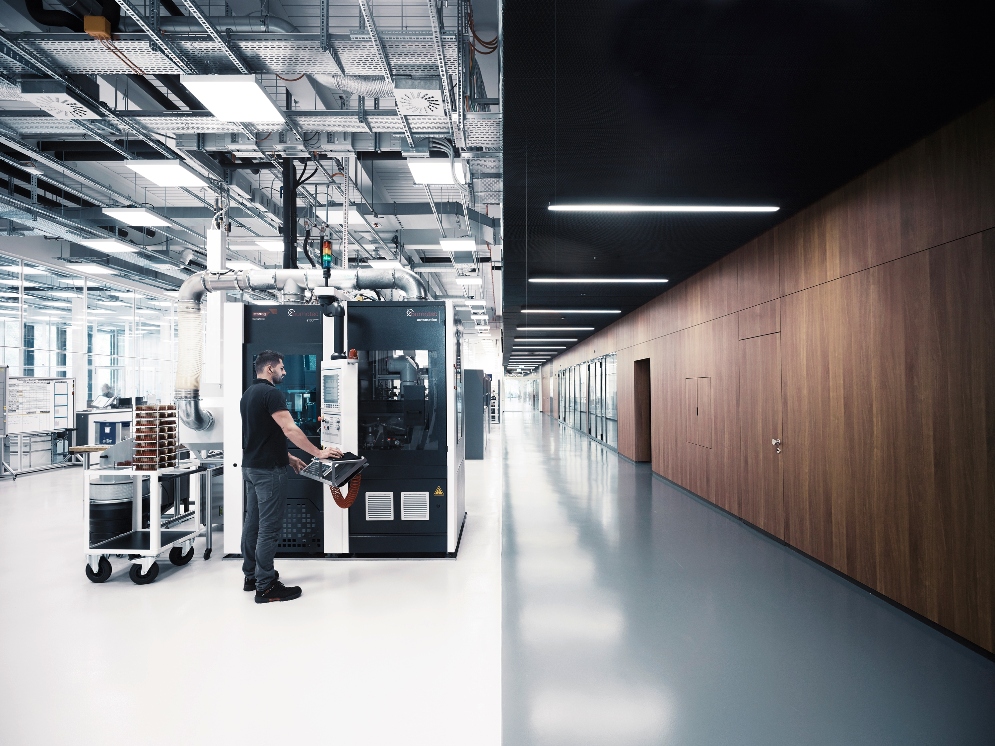
Most readers are aware that the majority of Swiss watches are made in the French speaking part of Switzerland. Some people who are unfamiliar with Switzerland and Swiss-made watches might think that the entire country is French-speaking. The Romandy is so dominant that a casual watch enthusiast might mistakenly think Schaffhausen to be a German town. IWC, on the other hand, is as Swiss as it gets. Since the manufacture is quite a ways off the beaten path, plenty of watch journalists actually miss out on visiting – getting here from Geneva is more challenging than getting to the La Chaux-de-Fonds, for example. When asked if we would like to visit during the summer, we were delighted.
I am referring to Ruckdee Chotjinda along with my IWC watches. It was only the second occasion I brought a watch home. Ruckdee had also brought his IWC, a Portugieser Perpetual Calendar made of red gold. Readers may remember that Walter Volpers, the IWC Manufacture Director, was on the same trip as me. I made it a point to mention the moment that he recognized our watches during the conversation.
The traditional evolution of manufacturing buildings is that they expand over time beyond the original confines. If you read the stories in this issue in order, you’ve already seen examples. IWC Schaffhausen – we will call it IWC in order to make the distinction between the brand name and the town easier – has been in the Old Town for a while. It is here that the brand’s offices are located, including the headquarters of the Communications team and CEO Christoph Herr-Granger. A small museum can also be found. It is also where a pivotal scene in this story will take place, starring Ruckdee’s watch. This will be revealed at the end, because there is a lot to cover in English, or as a Swiss German speaker might say, ‘quite a bit of ground to cover.
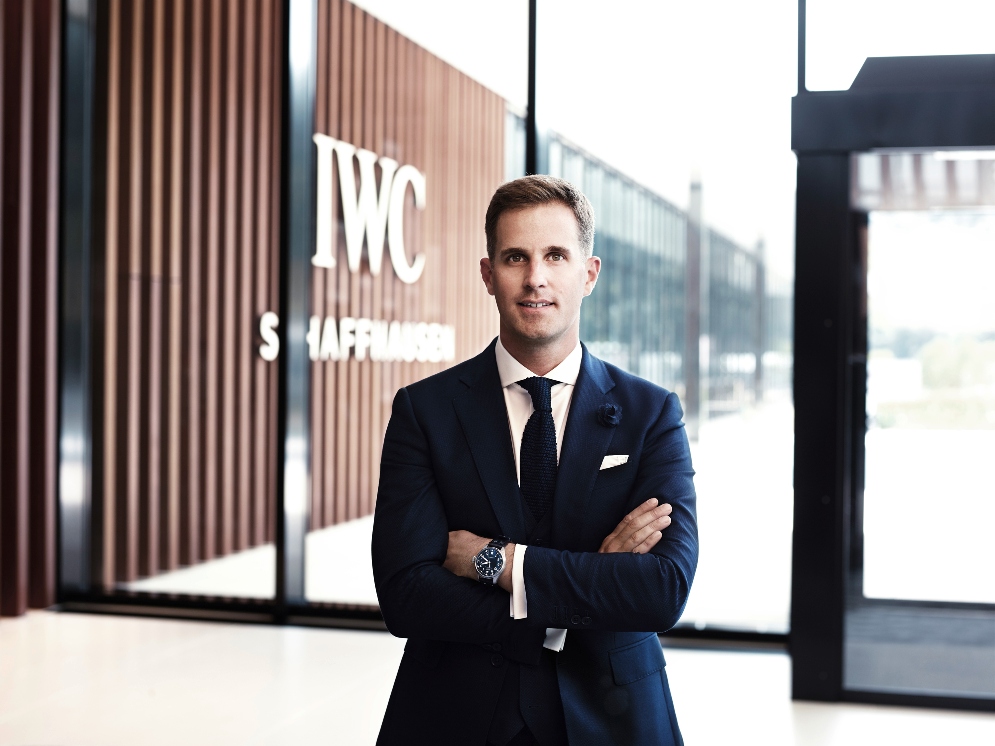
Imperative Presence
It was a good thing that the new facility we visited opened in 2018 as it was the 150th Anniversary of the brand. IWC now has options for how to meet the challenges of production in the future and in the present, just like Florentine Ariosto-Jones did in the past. The manufakturzentrum also happens to be an excellent workplace to visit, without much of the upstairs-then- downstairs-just-to-go-up-different-stairs hikes that are typical of many Swiss manufacturers. The existing office in the town will give you a good idea of this old reality. The completely new building boasts 13,500 sqm, as is evident from the spacious entry with its meters-high ceiling. It’s arranged in two levels.
The atmosphere is warm and welcoming. Everything is easy to understand, as there is a clear path for you to walk. In these images, the gray area is the place where visitors will walk. Meanwhile, the white area is the work space of the watchmakers, technicians, and engineers. This is a nice way to see everything and not feel guilty about invading people’s workspaces. The flip side of this is that you will not be able to peer over someone’s shoulder as he or she affixes a hairspring to a balance wheel. We are getting ahead ourselves.
It was only natural that we started with CNC machines because all the components are made this way. IWC’s Ingenieur collection is a professional-looking watch, and you can tell by the photos that IWC succeeded in this regard. Again, the downside is that the sense of homey craftsmanship is missing – production lines are production lines after all. The editor of Robb Report Singapore noted in his story about a visit to a modern manufacturer that the scent of oil still permeates the air. And the manufakturzentrum, as spick and span as it may be, is no exception. The industrial feel is appealing.
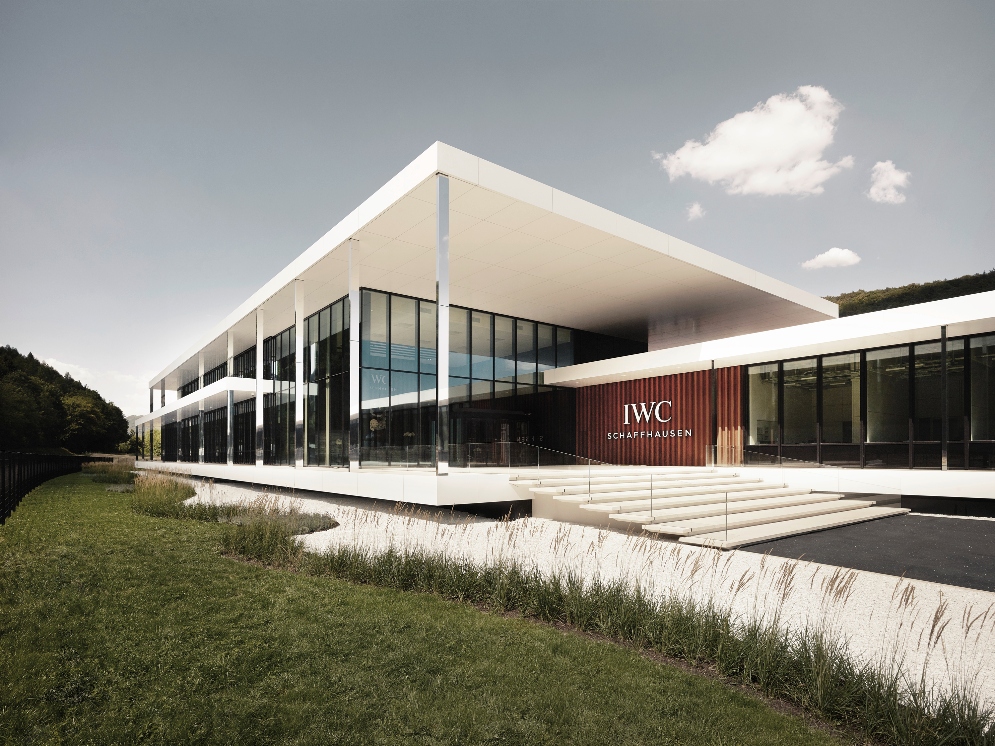
Maximum Punishment
We will take a moment to highlight a major point before we move on. In a very unusual tour, we were able enter the quality control room, where all kinds of torture devices are used to inflict maximum punishment to finished watches. Most reputable watchmaking shops do this, but you rarely get to see it. We enjoyed watching the team in this article, as noted in the Conversation in the Autumn issue. They used a heavy hammer to send watches into a net.
The idea behind quality control, or better yet, quality assurance, goes beyond the perverse pleasure that comes with causing damage to an expensive object. Instead, it is about proving the watches’ ability to withstand more than what you can do to them. IWC’s watches are tough as nails, and we can confirm that. IWC watches are not all tested in the same way, but samples from different production batches will be. The smiling technicians here are extremely thorough and enthusiastic about their work.
Moving back into the order of the tour proper, IWC takes pains to showcase its materials section, where there is that satisfying moment of holding rods of raw material in one’s hands. It is not an accident that the manufakturzentrum is home to a number of bar-turning, milling and other operations involving bars. IWC claims that around 1,500 components are produced in the workshop. It is reported that this includes all parts for calibre families 59 and 52 (manual winding with an eight-day power reserve), and 69 (automatic Chronograph). Included are also movement components, such as those for the Portugieser Grande Complication and its case. (This is done in the same basement where IWC makes all their other cases.
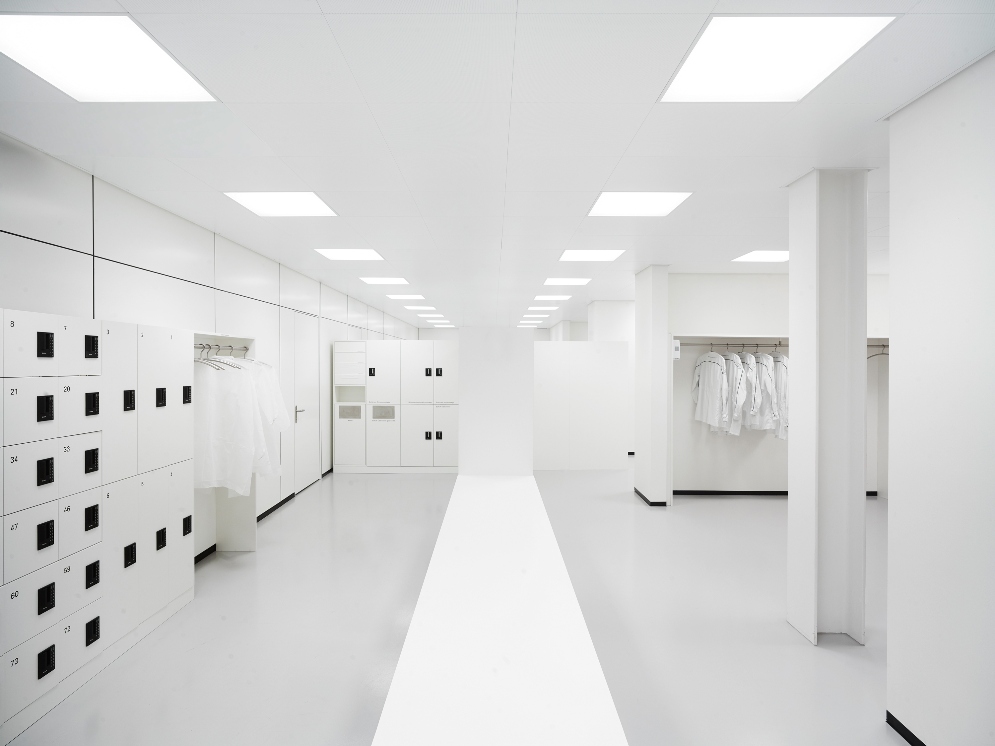
Assembly Required
The calibre 52 is a good example of this. A CNC machine produces the finished components after an articulated robotic feeds the raw materials. The assembly of complicated watches and components was not shown, but it is done in the manufakturzentrum. Robots do indeed assist in the assembly of movements, but the watchmakers are the ones who take over from the machine operators. IWC notes that production lines are in keeping with what founder Jones imagined in his time. It is safe to say that nobody in the 19th century would have thought of 21st century engineering methods! Though we won’t be focusing on this, one metre of material is enough to make between 30 and fifty cases. (Depending on the material and type of case. According to Time and Tide).
The final part of our tour took us back to the beginnings of watchmaking, as we disassembled and assembled a generic pocket-watch movement. This was once a standard of factory tours, but the IWC visit was the only time we saw it. It is always an eye-opening and fascinating experience to see how tiny machines are assembled from tiny parts. We strongly recommend that all manufacturers return to this tradition, if for no other reason than context.
The activity of producing calibres in-house is done in a clean room, which is the norm for modern manufacturers. The guests and journalists are unable to see the assembly process, which is why we believe that the importance of watch assembly activities. The clean room environment that manufacturers have is different from what you would find in silicon wafer production, for example. But it’s close.
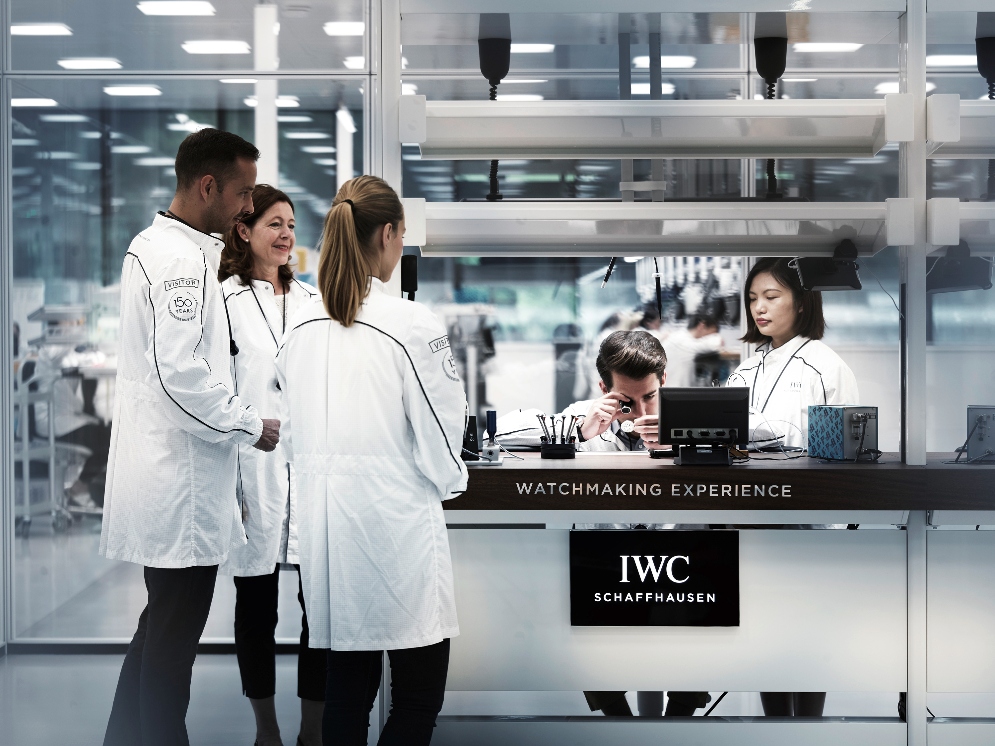
Personal Touch
The manufakturzentrum is our last thought. It is an impressive structure, and it is sure to reflect IWC’s character. Its massive windows provide an abundance of natural lighting for the watchmakers who assemble movements. It’s not by accident that the entire building feels too large. The structure can house up to 400 people (currently there are 230 employees here), and was designed for the long-term. The manufakturzentrum, designed by Zurich architects ATP was also personally designed by CEO Herr-Granger.
The manufakturzentrum also represents sustainable practices, as it has solar panels on its roof, and uses groundwater for heating and cooling. The history of IWC is also reflected in this, with founder FA Jones selecting Schaffhausen partly due to the hydroelectric power provided by the Rhine river.
On that note, it is time to return to Ruckdee’s watch, which had a bit of an issue – residue of oil leftover from servicing, on the hands. After inspecting the watch, the IWC watchmaker asked Ruckdee simply to leave it in his hands and come back later. Ruckdee seemed to be pleased with the outcome. It is clear that the human element makes all the difference in the world, regardless of the technology that goes into the watches.
This article was first published on WOW’s 2024 Legacy Issue
Click here to learn more about the latest.